This is part of our Ultimate Guide to Private Label Probiotics, a complete overview of the benefits of probiotic supplementation for consumers, some of the different strains and their specific uses, the process of responsibly manufacturing a probiotic product, and what to look for when choosing a probiotic manufacturer.
As we discussed in our last post on manufacturing essentials for private label probiotics, the delicate nature of probiotics requires that they be handled with care throughout the manufacturing process. To ensure a viable, successful finished product is created, it is important to make sure that quality control (QC) is involved at critical stages of the process.
Raw Probiotic Strains Processing
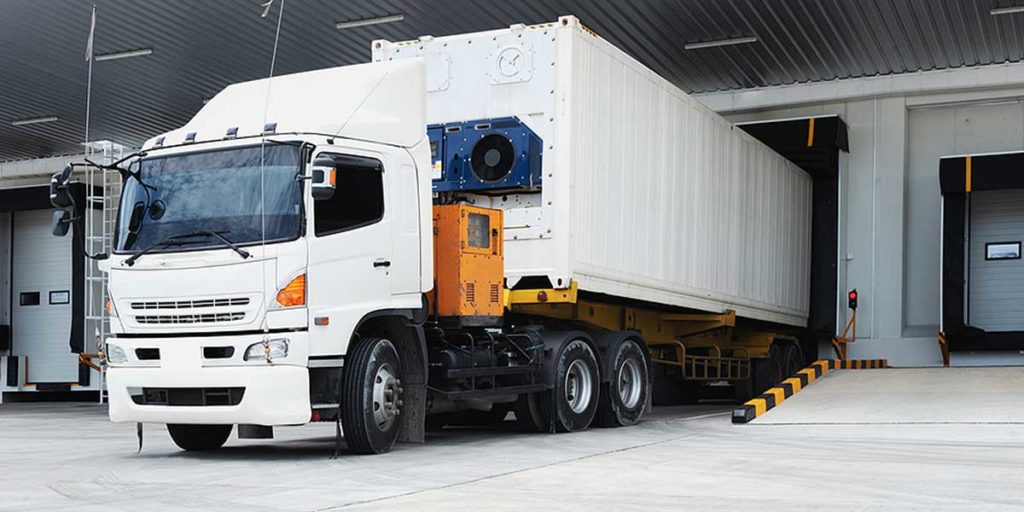
Following GMPs (good manufacturing practices) for successful private label probiotic manufacturing begins with the assurance that the probiotic raw materials meet the required quality standards of identity, potency, and purity.
As soon as the probiotics arrive at the manufacturing facility, the delivery truck should be inspected by a receiving team checking for general cleanliness, hazardous chemicals, pests, and temperature.
The live probiotic material will be taken off of the truck, removed from any outer packaging and immediately put into a refrigerated area, and samples of the raw materials will be taken for aside for testing.
Once the samples are approved by QC, the material will be released to a different location in the refrigerated unit to be counted as raw material inventory.
Probiotic Supplement Production
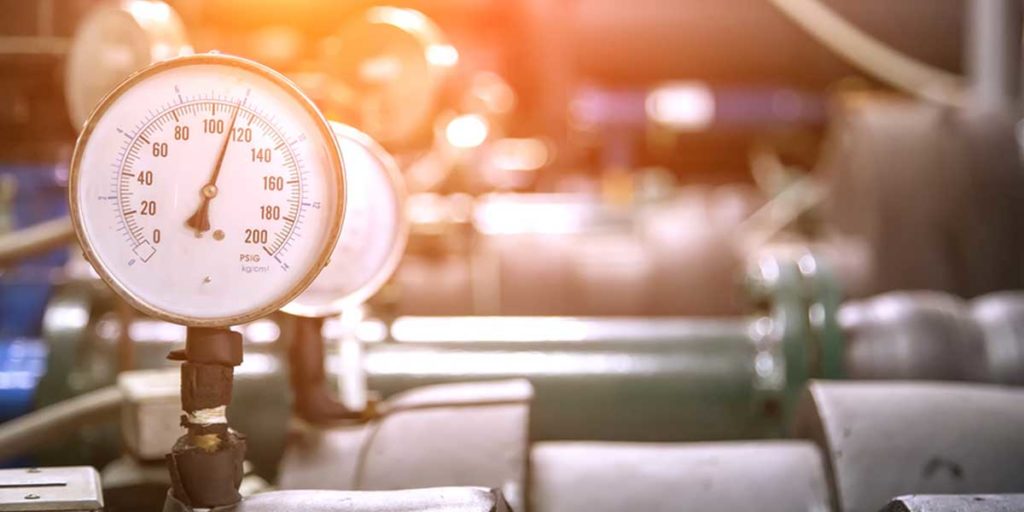
During the process of formulation, R&D determined which ingredients should be included in order to achieve the desired health benefit. A private label probiotic might be a single-strain product, targeting one specific benefit, a multi-strain product, offering multiple benefits, or a more complex formula, such as a protein powder that also includes probiotics for added benefit.
Whichever type of product the probiotics end up going into, Quality Control will be involved to guarantee three important results:
- Safety – During manufacturing, the high microbial counts of the probiotic raw materials could present a risk of contaminating the air, manufacturing rooms, surfaces, equipment or other products within the area, so appropriate moisture control, cleaning, and sanitation protocols must be adhered to while they are being processed.
- Viability – The product will be formulated using an effective starting dosage (CFUs), incorporated with a suitable overage, to ensure viability through expiration date. Additionally, appropriate climate-controlled conditions will be monitored and maintained during manufacturing to ensure the vitality and health of the organisms.
- Stability – Depending upon the type of finished product they will become, appropriate protocols will be followed to prevent conditions that may negatively impact the stability of the finished product. For example, probiotic bacteria in dry powder form are hibernating. They are essentially dormant and need to be kept that way until they are either consumed or added to a liquid product (such as when in a protein powder) and activated by moisture.
Samples will be taken throughout the manufacturing process, monitoring the potency and enumeration (as measured in CFUs) of the probiotics and to ensure no cross-contamination has occurred.
Finished Probiotic Supplement Testing
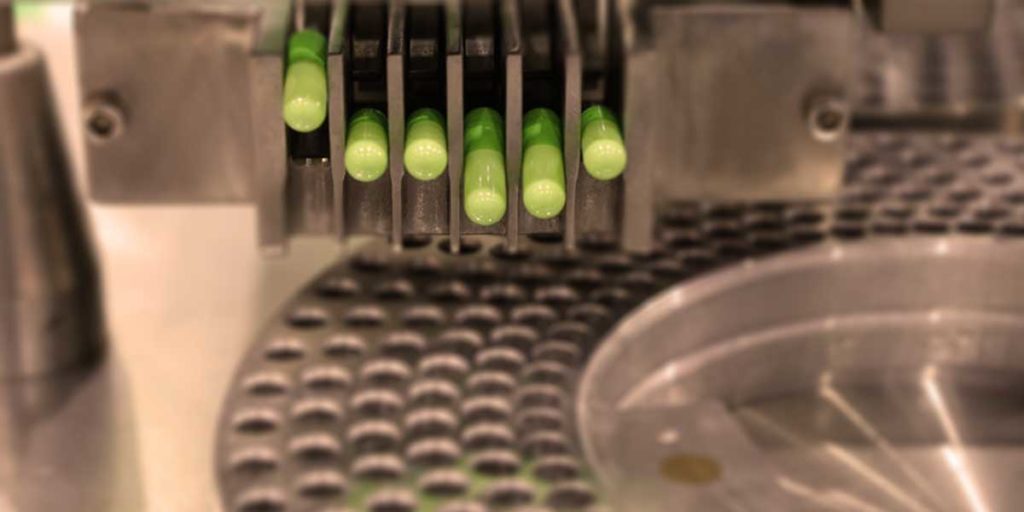
Once production of probiotic supplements are complete and they are in their final form, finished product stability testing begins.
Internal Probiotic Stability Testing
Stability testing of finished products is necessary to determine the projected lifetime and expiration date. The number of days that the product remains stable at appropriate storage conditions is referred to as the “shelf life” of the product.
There are two main types of stability testing: Real-Time Stability testing and Accelerated Stability testing. Which type of testing is used can be a significant point of differentiation between different probiotic brands and their manufacturers.
In Real-Time Stability testing, a product is retained at recommended storage conditions and monitored at specific time points such as 6 months, 1 year, 2 years, or even up to 5 years. Products in storage will change as they age, especially product with live organisms inside them, but they are considered to be stable as long as their characteristics remain within the manufacturer’s specifications. This real-time data provides an accurate measure of how viable the product will be from the time it was made until its expiration date.
Accelerated Stability testing is a modified method used to quickly estimate the life span of a product when real-time data is unavailable, such as with a new product. The finished product is subjected to an elevated level of stress, such as controlled changes in temperature or humidity, to mimic similar conditions the product may have experienced over a certain timeframe. While it is true these studies can help to provide labeling information in a short timeframe, they are not as accurate in determining the real-time performance and viability of the probiotic product, therefore should not be used as the only testing method.
Some companies will only perform accelerated stability testing, usually in an effort to get a new product to market as quickly as possible. That is often the reason the CFU count on a product is listed “at time of manufacture”, rather than “through expiration date”. This does not provide clear information to the consumer of how many cells are still viable when they are taking the product a month after it has been manufactured, or six months after that when it is at home with them.
Third-Party Probiotic Supplement Testing
Third-Party Testing is another important testing method. Even though an experienced probiotic manufacturer will have their own in-house lab, they should also employ the services of a “third party” testing facility. These independent third-party labs are an additional resource in making sure to verify the private label probiotic finished product contents and identity, to confirm that the product was manufactured in consistent, compliant conditions, and in some cases to ensure the product label is accurate and compliant with regulatory standards.
A third-party lab is basically an impartial expert that can validate the finished product is exactly what the label claims it is. Once all of the internal and third-party testing and data collection have been completed, the manufacturer will release the finished product to be sold by their private label customers.
Summary
There are many companies looking to capitalize on the current demand for probiotic products who do not understand the challenges associated in manufacturing with probiotic ingredients. Therefore, choosing an experienced private label probiotic manufacturer to work with is critical to creating and offering a beneficial probiotic product.
Key Takeaways:
- Probiotics need to be tested frequently throughout their journey to becoming finished products.
- Successful private label probiotic manufacturing begins with the assurance that the probiotic raw materials arrive to the facility properly identified, healthy, and clean from contaminants.
- While accelerated testing can be useful, real-time stability testing is the most accurate way to determine the shelf life of a probiotic supplement.
- It is important to work with an experienced probiotic manufacturer who employs the necessary Quality Control testing and methodology protocols.
➤ Learn More About Selecting the Right Manufacturer for Private Label Probiotic Supplements
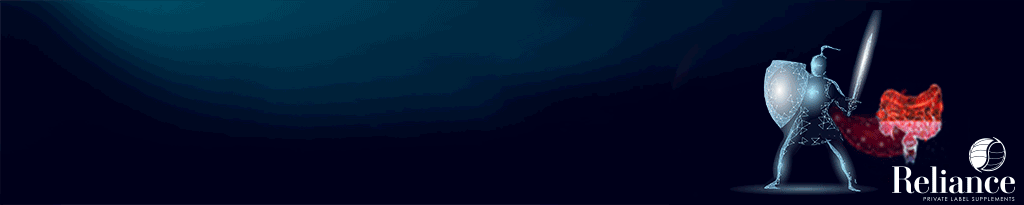
†These statements have not been evaluated by The Food and Drug Administration. This product is not intended to diagnose, treat, cure or prevent any disease.